Torque Converter, 2,400-2,800 Stall, 4L60/65/70/75-E, Late LS V-8 trans. Mates to Early Gen 1 SBC/BBC, Dual Bolt Pattern, 10.75 and 11.50 in. The 4L60 however is hydraulically shifted based on governor pressure and throttle valve (TV) cable position. 1992 was the last year of widespread usage of the 700R4 (4L60). The 1993 Camaro, Corvette and Typhoon were equipped with the last production 700R4. The last design change of the 700R4 was an added checkball to the valve body.
Turbo-Hydramatic | |
---|---|
Overview | |
Manufacturer | General Motors |
Production | 1964–2012 |
Body and chassis | |
Class | 3-speed longitudinalautomatic transmission |
Related | Turbo-Hydramatic 125 Turbo-Hydramatic 180 Turbo-Hydramatic 425 |
Chronology | |
Predecessor | Dynaflow Hydra-Matic Powerglide Jetaway Super Turbine 300 |
Successor | 4L60-E/4L65-E 4L80-E/4L85-E |
Turbo-Hydramatic or Turbo Hydra-Matic is the registered tradename for a family of automatic transmissions developed and produced by General Motors. These transmissions mate a three-element turbinetorque converter to a Simpsonplanetary geartrain, providing three forward speeds plus reverse.
The Turbo-Hydramatic or Turbo Hydra-Matic (THM) series was developed to replace both the original Hydra-Matic models and the BuickDynaflow. In its original incarnation as the Turbo-Hydramatic 400, it was first used in the 1964 model year in Cadillacs. The Buick version, which followed shortly thereafter, was known as the Super-Turbine 400. By 1973, THM units had replaced all of GM's other automatic transmissions including Chevrolet's Powerglide, Buick's Super Turbine 300, and Oldsmobile's Jetaway. Starting in the early 1980s, the Turbo-Hydramatic was gradually supplanted by four-speed automatics, some of which continue to use the 'Hydramatic' trade name.
4l60e Transmission
Although the Turbo Hydra-Matic name alludes to the original Hydra-Matic developed by General Motors' Cadillac division in the late 1930s, the two transmissions were not mechanically related.
Super Turbine 400 / THM400 / THM375 / 3L80 / 3L80HD[edit]

The THM400 can be visually identified by an oil pan number four shown at General Motors Transmission Pans. First introduced for the 1964 model year under the name 'Turbo Hydra-Matic' in Cadillacs and 'Super Turbine' in Buicks. The following year, application expanded to Oldsmobile and Pontiac and to some full-sized Chevrolets. Many of the Buick, Cadillac, and Oldsmobile THM400s produced between 1964 and 1967 were equipped with a 'Switch-Pitch' torque converter with a variable-pitch stator, which is sought after by collectors and drag racers. These can be identified outside the vehicle (with the torque converter removed) by a narrow front pump spline. Externally the switch pitch version has two electrical connections, where the non-switch pitch THM400 has only one. GM used a Switch Pitch torque converter in the Buick twin turbine Dynaflow transmission between 1955–1963 and the Super Turbine 300 two speed transmissions used by Oldsmobile, Pontiac (Pontiac's ST300 didn't have a switch pitch), and Buick divisions between 1964 and 1967. This transmission (among other THMs) is identified by the 'Park R N D L2 L1' selector quadrant. The switch pitch is not the only THM400 that utilizes an external 2 prong connector. Other units to include the 2 prong connectors had an internal pressure switch that was used to control spark timing retard. All THM400 units had a 32 spline output shaft with the exception of the THM375 that used a 27 spline output.
.jpg/1200px-Ypsilanti_Automotive_Heritage_Museum_May_2015_065_(Hydra-Matic_4T80_transmission).jpg)
A variant of the THM400 known as a THM375 is a THM400 with a mid length 27 spline output shaft that mates to the smaller THM350 27 spline drive shaft yoke. It can be identified by '375-THM' cast into the tailhousing. Internally the clutch packs originally had fewer friction plates. THM375s were found in some 1971-76 Buick Lesabres and Oldsmobile Delta 88s with the 5.7 liter V-8. Somewhere in the Mid-80's Chevrolet C10 Pickups could also come equipped with a THM375. It is a THM400 Chevrolet bolt pattern case that has a longer 27 spline output shaft and matching extension housing with 'TH375' cast into the housing. Some 'Heavy Duty' THM350s were also designated THM375-B. Another variant is the 3L80HD, often referred to as a Turbo 475. The 3L80HD has a straight-cut planetary gear set. There is no externally visible way to determine whether the transmission contains the straight-cut planetary gear set. The THM425 front wheel drive transmission shares almost all its internal parts with the THM400. Checker Motors Corporation Motor Company used the Chevrolet version of the THM400 for its 'A' series taxi and Marathon models until the end of production in 1982.
By 1980, the relatively heavy THM400 was being phased out of usage in passenger cars in response to demand for improved fuel economy. The THM 400 was utilized in the C- and K-series (full-size) Chevrolet/GMC pickups and G-series (full-size) vans until 1990 when GM switched over to the 4L80E. Today, the United States ArmyHMMWV is the only vehicle using the THM400. The civilian Hummer H1 originally had the 3L80s, but the current model has had a 4L80E since the mid-1990s.
Through the end of the '70s substantially more CBOP (Cadillac/Buick/Oldsmobile/Pontiac) bellhousing THM400s were produced than any other THM400. Chevrolet bellhousing THM400s, while not rare, can be hard to find and are, as a result, usually more expensive to buy (they were commonly found in 3/4 ton (8500 GVW and above) Chevrolet/GMC trucks and vans (includes the P-series box vans and 1983-86 CUCVs) when RPO M40 was checked off the option list - especially when coupled to a 454 - usually in HD applications including the C40-C60 medium duty trucks where a bolt-on output shaft is used in place of a slip yoke) - when used with passenger cars it was usually coupled to a Mark IV engine or some high performance small blocks (e.g. the 1970 LT-1). The THM400 was never produced with a multicase bell housing.
Other auto manufacturers have used the THM400 and its 4L80E successor, including Ferrari (in the 400/412); Jaguar/Daimler (in pre-1994 XJ12 and XJ-S coupes and their Daimler stable mates); Rolls-Royce (in 1965–1980 Silver Shadow and 1980-1992 Silver Spirit series cars, along with their Bentley stable mates); the Nissan Prince Royal; AM General; and Jeep (usually found in the FSJ pickups and SUVs). Early Jeep THM400s used an adapter between the engine and transmission bell housing while later models had an AMC specific housing - which bolted to its inline six and V8. Though identical except for the bell housing pattern used through the '60s and ending in 1979 the THM400 was mated to the Dana model 18,20 and was the only transmission used with the Borg-Warner 1305/1339 all-wheel-drive transfer case used only in Jeeps (AMC/Jeep phased in the used of the Chrysler Torqueflite 727 after 1979 until the FSJ platform was phased out), It has been known to adapt a THM400 to other engines using adapters.
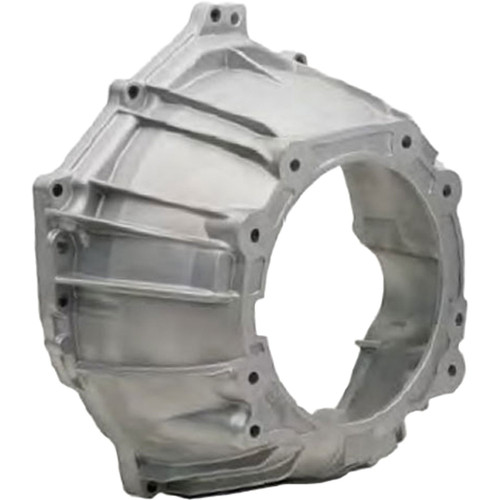
THM400 transmissions are very popular in automotive competition due to their great strength. Much of this strength comes from the use of a cast iron center support to suspend the transmission's concentric shafts that join the clutch assemblies to the gear train. The center support, which is splined to the interior of the transmission's case, also provides a robust reaction point for first gear (the gear train's reaction carrier is restrained from counter-rotating the engine in first gear by a roller clutch whose inner race is part of the center support). Since the first gear reactive force is evenly distributed around the periphery of the case, the types of mechanical (and some times violent) failures that have plagued other competition transmissions[vague] are rare.
The THM400 was the first three-speed, Simpson-geared automatic to use overrunning clutches for both first and second gear reaction, a feature that eliminated the need to coordinate the simultaneous release of a band and application of a clutch to make the 2-3 gear change. Owing to this feature, as well as the use of a large, multi-plate clutch to provide second gear reaction, the THM400 is able to withstand very high input torque and an enormous number of shifting cycles, as would be encountered in frequent stop-and-go driving. As a result, it has met with considerable success in commercial vehicle applications.
For 1987, GM changed the nomenclature of their Turbo Hydramatic transmissions — the THM400 was renamed '3L80' (three forward speeds, longitudinal positioning, and an arbitrary strength rating of 80, the second highest such rating assigned). The 3L80HD was introduced in 1987 as the HD unit used in passenger trucks. In 1991, a four-speed overdrive version, the 4L80-E, replaced the THM400 in Chevrolet/GMC pickups, vans, SUVs, and commercial vehicles. The 4L80E (and its successor 4L85E) was the first Hydramatic to incorporate electronic controls — almost all of the THM400/3L80/3L80HD's components are interchangeable.
Transmission fluid cooler line connections are found on the right-hand side of the THM400. The lower connection is the cooler feed, and the upper connection is the return.[1] The case is tapped for either self-sealing 1/4'NPT fittings, or 1/2'UNF fittings with a washer seal. 5/16' or 3/8' rigid coolant lines are generally connected via appropriate double-flared adapters.
Four-wheel drive truck applications used 3 various shorter output shafts that coupled with a female transfer case input shaft. Early transfer cases mated directly to the THM400 with a cast-iron adapter, usually a vertical oval shape. Later models used a circular style iron adapter which is generally considered the stronger of the two. The shortest was used with the NP203 transfer case.
Gear | Ratio |
---|---|
1 | 2.48:1 |
2 | 1.48:1 |
3 | 1.00:1 |
R | 2.07:1 |
THM350[edit]
The Turbo Hydra-matic 350 was first used in 1969 model cars. It was developed jointly by Buick and Chevrolet to replace the two-speed Super Turbine 300 and aluminum-case Powerglide transmissions. So, although it carries the Turbo Hydra-matic name, the Hydra-matic Division of General Motors had little, if anything, to do with its design. The 350 and its 250, 250C, 350C and 375B derivatives have been manufactured by Buick in its Flint, Michigan plant, and by Chevrolet in Toledo and Parma, Ohio and Windsor, Ontario.
The THM350 was also regarded as a 'three speed Powerglide' and during its development, was generally called this. Although it uses the same torque converter as the THM400 (without variable pitch stator) it has a familial resemblance to the 1962-73 aluminum Powerglide from Chevrolet[according to whom?] and was largely derived from the Chevrolet design. An important difference in the THM350 compared to the THM400 is that there is no fixed center support midway through the geartrain; this difference in layout would have permitted the THM350 to be adapted to the Corvair where the drive and driven ends are the same, but this feature was not exploited. Air-cooled versions (with a baffle on the torque converter and air intakes cast into the bellhousing) of the THM350 appeared mid-1972 in the Chevrolet Vega and Nova 6.
One THM350 weak point was excessive end-play between the pump and center support and resulting wobble of the direct clutch drum due to both the end play and use of a relatively narrow bushing in the drum. This weak point can be addressed by using an extra thrust washer between the planetary gear and direct clutch to remove the end play and using a wider aftermarket bushing in the direct clutch drum.[according to whom?] Another weak point is the relatively thin center support and the lightweight matching splines in the case. This weakness can be addressed by using an inexpensive aftermarket case saver kit.
Open source software download for mac. Four-wheel drive truck applications for the THM350 used an iron adapter that mated it to the transfer case directly, similar to the THM400. The THM350 adapter was cast iron and used a sliding sleeve to couple the transmission output shaft to the transfer case input shaft with a steel coupler sleeve that was splined to accept both shafts and couple them together. An internal snap ring inside the coupler sleeve controlled the sleeve's position on the shafts, with circular seals in the adapter sealing the transmission from the transfer case.
For the 1981 model year, a lock-up torque converter was introduced which coincided with the new EMC control of most GM cars; this version is the THM350-C, which was phased out in 1984 in GM passenger cars for the 700R4. Chevrolet/GMC trucks and vans used the THM350-C until 1986. The lock-up torque converter was unpopular with transmission builders B&M Racing once marketed a conversion kit for THM350-Cs during the early 1980s until the advent of high stall lock-up torque converters when its overdrive counterpart (THM700R4/4L60) were modified. The standard TH350 is still very popular in drag racing.
THM250[edit]
The THM250 is a derivative of the THM350 and was introduced for 1974 in Chevrolets as a Powerglide replacement. Internally, the THM250 is a THM350 without the intermediate clutch pack and with a band adjuster similar to the Powerglide. The THM250 was usually coupled to smaller displacement engines - the largest a third generation Chevrolet inline six found in the Nova and Camaro (1974 and 75 model year only). During the 1976 model year the THM250 was phased out of production, replaced with the lighter duty THM200. It was later reintroduced in 1979 as the THM250-C in the wake of the failure-prone THM200/200C - the later 250C was further lightened with the use of a sun gear shell used with the THM350 but with 3 holes to reduce rotating mass and the low/reverse piston with 8 cutouts.
Gear | Ratio |
---|---|
1 | 2.52:1 |
2 | 1.52:1 |
3 | 1.00:1 |
R | 2.07:1 |
THM200[edit]
After the 1973 OPEC oil embargo, GM developed a lighter-duty version of the THM350 with lightened materials — primarily alloys in place of ferrous materials (e.g. clutch drums and oil pump) — the Turbo-Hydramatic 200. The THM-200 was first used in 1976 models including GM's T-cars (which includes the rebadged Isuzu Gemini sold through Buick dealers as the Buick/Opel by Isuzu), X-cars, and some Isuzu automobiles (Chevrolet LUV and Isuzu P'up). However, this transmission was notorious for its failure rate[citation needed] when used behind too large an engine - the largest being the Oldsmobile 5.7 L diesel. No multicase bellhousings were used - bellhousing patterns included Chevrolet V8, Buick-Oldsmobile-Pontiac, Vega 4, GM 60 degree pattern (includes the Tech IV), and Isuzu G engine.
It was GM's first transmission which used a throttle valve cable (similar in design to the Chrysler Torqueflite part throttle kickdown linkage) controlling the shift points and part throttle kickdown. This setup was later incorporated into the THM700R4.
Starting with the 1979 model year, vehicles which had the THM-200/200C as standard equipment were optioned with the THM250-C, which is a THM-350 without the intermediate clutch pack along with an adjustable band similar to the Chevrolet Powerglide. Also in the 1979 model year, the THM-200 received a lockup torque converter, and some internal components (primarily the low/reverse clutch drum and planetary gears) were later shared with the Turbo-Hydramatic 200-4R. The low/reverse sprag (roller clutch) assembly was also shared with the 1988-04 Chrysler Torqueflite 904 (also 30, 31, 32RH) and its derivatives e.g. the A500 and 42RE. THM200/200Cs were produced until 1987.
Gear | Ratio |
---|---|
1 | 2.74:1 |
2 | 1.57:1 |
3 | 1.00:1 |
R | 2.07:1 |
THM200-4R[edit]
For the 1981 model year, the 200-4R was introduced. The components which were prone to failure in the THM200 were improved, and in the later 1980s this transmission was used with high-power applications — primarily the Buick Grand National and the 1989 Pontiac Firebird Trans Am Indy 500 Pace cars. The 200-4R was configured with several different torque converters depending on the vehicle application.
Unlike the 700R4, most 200-4Rs have a multicase bellhousing for use with Chevrolet, Buick/Olds/Pontiac (BOP), and Cadillac engines. However, 200-4Rs share mounting locations with the TH-400. Since the external dimensions are similar to the TH-350 (overall length, drive shaft yoke spline count/diameter and general size), 200-4Rs are often swapped in place of TH-350s in older vehicles to provide an overdrive gear. Early models had a 'PRND321' shift indicator, while later models used 'PRN(D)D21,' with the left D identified as the overdrive gear by a square or oval ring.
The THM200-4R can be found in the following vehicles: Download azure storage explorer tool.
- 1981-90 B-bodies
- 1981-84 C-bodies
- 1983-88 G-bodies
- 1985-90 D-bodies
- 1989 Pontiac Firebird Trans Am Indy Pace car (with Buick V6 and a turbocharger)
The THM200-4R was phased out after 1990; its final usage was in the GM B-body vehicles.
Gear | Ratio |
---|---|
1 | 2.74:1 |
2 | 1.57:1 |
3 | 1.00:1 |
4 | 0.67:1 |
R | 2.07:1 |
THM700R4 / 4L60 / 4L60E / 4L65E / 4L70E[edit]
The four-speed Turbo Hydra-Matic 700R4 was introduced for the 1982 model year for use in Chevrolet/GMC vehicles.
In 1990, the Turbo Hydra-Matic 700R4 was renamed the 4L60. Under the new designation, the '4' stands for the number of forward gears, the 'L' for longitudinal applications (rear-wheel-drive), and the '60' is the strength rating (less than the 4L80). '60' is the relative torque value. For example, 80 is stronger than 60, which is stronger than 40, etc. A 4L80-E can handle more torque than a 4L60-E. The 'E' denotes electronically controlled shifting. The 4L60 however is hydraulically shifted based on governor pressure and throttle valve (TV) cable position. 1992 was the last year of widespread usage of the 700R4 (4L60). The 1993 Camaro, Corvette and Typhoon were equipped with the last production 700R4. The last design change of the 700R4 was an added checkball to the valve body. In 1992 electronic controls were added, and it became the 4L60-E. The 4L60E is not easily swapped with the 4L60, as the 4L60E depends on a powertrain control module (PCM) to shift.[2] The 4L60E went into service in trucks, vans, and SUVs in 1993 and in all RWD passenger cars (Corvette, F and B/D bodies) in 1994. In 2001, an updated version — the 4L65-E, was introduced. Five-pinion planetaries, along with a strength-improved output shaft, were improved to withstand the 300+ lb·ft (400+ N·m) of torque of the 6.0 Vortec engine.The 4L70E transmission is the same as a 4L65E with a speed sensor located in the pump.
700R4 / 4L60 / 4L60E / 4L65E / 4L70E / technical description[edit]
The Turbo Hydra-Matic 700R4 can be identified by an oil pan number six shown at General Motors Transmission Pans.
The tailshaft housing is held onto the main case by four bolts (the bolt spacing is similar to the THM350), and uses a square-cut o-ring seal, and not a gasket. The typical width of this transmission where it bolts to the engine is 20 in (51 cm) overall. From the engine/trans mating surface to the cross member mount bolt is 22.5 in (57 cm), and engine/trans surface to output shaft housing mating surface is 23.375 in (59.37 cm) overall, with the tail shaft housing typically measuring 7.625 in (193.7 mm). External dimensions are similar to a THM350 with a 9-inch tailhousing found in Chevrolet/GMC long wheelbase truck/vans and 1971-76 B-bodies (Bel Air, Impala, Caprice).
Transmission fluid cooler lines on the 700R4 the bottom fitting on the right side of the transmission is the 'out' line to the cooler and the top fitting is for the return line from the cooler. These fittings are .25 in (6.4 mm) pipe thread, and can include an adapter from the factory for threaded steel lines in a SAE size. 4L60Es manufactured after 1995 use snap-in connections instead of threaded. The original version of the transmission had a 27-spline input shaft (shared with the THM200C and 2004R) which was a common failure point. In 1984, the 700R4 designed for use behind Chevrolet small block V8s received a 30-spline input shaft similar to those found on TH400 transmissions and which also used a different torque converter than its 2.8 V6 and 2.2 L4 engines. Between 1984 and 1987, internal components, from the ring gear to the oil pump housing, were updated, ending with the auxiliary valve body for 700s manufactured after October 1986.
In 1995, the 4L60E received a PWM-controlled lockup converter. The early designs simple on or off lockup function while the later design can variably lock as to not feel the lock up occur. GM added a fifth solenoid to the valve body, called the PWM solenoid. In 1996, GM introduced a redesigned 4L60E transmission case that incorporated a bolt-on bellhousing and a six-bolt tail housing. This two-piece case style was first seen in 1996 and up model S-10 Blazer, S-10 pickup, GMC Jimmy, and GMC Sonoma with the 4.3 L engine. The majority of 1998 and later applications of the 4L60E were two-piece cases (i.e. a removable bellhousing). Both transmissions are the same internally. The non-PWM (1993-1994) style 4L60Es are not interchangeable with PWM-style (1995 and later) 4L60Es. Also in 1996, GM changed the 3-2 solenoid to a different style which makes it not interchangeable with any previous models. For the model year 1996 GM trucks, there were two versions of the 4L60E: one had a bolt-on bellhousing, the other did not. The bolt-on bellhousings used on the 4.3 L V6 and 1996-2002 GEN I+ versions of the small-block Chevrolet V8 used the same bellhousing, while the LSx engines used a longer one to accommodate a redesigned torque converter with a longer pilot nose (GM sells an adapter assembly for using the LSx 4L60Es when used with an early engine).
Gear | Ratio |
---|---|
1 | 3.059:1 |
2 | 1.625:1 |
3 | 1.00:1 |
4 | 0.696:1 |
R | 2.29:1 |
700R4 / 4L60 / 4L60E / 4L65E /4L70E applications[edit]
[3][4]
- 1982-1992 Chevrolet Blazer/GMC Jimmy
- 1982-2005 Chevrolet Corvette
- 1983-1996 Chevrolet Impala and Caprice police specials equipped with 350 engines.
- 1983-1985 Oldsmobile 350 Diesel equipped models.
- 1983-2002 Chevrolet Camaro/Pontiac Firebird
- 1985-2005 Chevrolet Astro/GMC Safari
- 1991-1992 GMC Syclone
- 1991-1992 Oldsmobile Custom Cruiser
- 1989-2003 Chevrolet S-10/GMC S-15/Sonoma
- 1989-2005 Chevrolet S-10 Blazer
- 1989-2001 GMC S-15 Jimmy
- 1990-1996 RWD Cadillac Fleetwood/Cadillac Brougham/Cadillac Limo
- 2002-2009 Chevrolet TrailBlazer/GMC Envoy
- 1992-1993 GMC Typhoon
- 1984-2010 Chevrolet Suburban
- 1982-2012 Chevrolet Van
- 1994-1996 Chevrolet Impala
- 1994-1996 Buick Roadmaster
- 1982-2010 Chevrolet C/K
- 1993-2010 Chevrolet Tahoe/GMC Yukon
- 1999-2006 Cadillac Escalade
- 2002-2008 Chevrolet Avalanche
- 2003-2007 Hummer H2
- 2004-2007 Buick Rainier
- 2004-2012 Chevrolet Colorado/GMC Canyon
- 2002-2009 GMC Envoy
- 1988-2006 Holden Commodore
- 2003-2008 Isuzu Ascender
- 2004-2006 Pontiac GTO
- 2005-2009 Saab 9-7X
See also[edit]
References[edit]
- ^Sessions, R (1987). How to Work with and Modify the Turbo Hydra-matic 400 Transmission, ISBN0-87938-267-8, p. 108
- ^'700R4 Transmission Resource'. 700R4 Transmission Resource. Retrieved 2016-06-27.
- ^Chevrolet/GMC/Geo Transmission Lookup Table, http://www.autorepairmanuals.biz/site/573683/page/372807
- ^Transmission Application Chart, 'Archived copy'. Archived from the original on 2008-01-01. Retrieved 2007-12-21.CS1 maint: archived copy as title (link)
External links[edit]
TRANSMISSION INSPECTION and ASSEMBLY
Inspect all gears, pinions, and carriers for signs of wear, galling, or other damage. Replace parts as necessary. Closely inspect the splines in all locations, specifically the reaction sun shell hub and mating reaction sun gear spline, the reaction carrier hub spline, input sun gear, and the 1-2 planetary ring gear carrier hub. Any signs of damage or cracking in the carriers should indicate a need for replacement.
Inspect the low-reverse clutch steels and clutch discs. Any signs of heavy scuffing or burning should indicate replacement. If the steels are intact, they can be cleaned and lightly honed, stoned flat, or ground to break any surface glazing. Inspect the reverse clutch spring pack and springs for damage, distortion, or breakage. Replace any parts as necessary. Any clutch plates installed new or after solvent cleaning must be soaked in clean transmission oil before assembly.
Assemble the low-reverse support plate and clutch stack on a flat surface and check the overall thickness of the stack at its extreme outer edge. If the dimension is below 1.200', the steels and/or clutch plates should be replaced. If the dimension is between 1.200' and 1.240', it is acceptable. Install the clutches into the case.
Test the reverse sprag clutch operation. It should rotate with some amount of light resistance in the clockwise direction, and not rotate in the counterclockwise direction at all.
Assemble rear input planetary set, sprag clutch, support plate, and large lock ring in reverse order of disassembly.
Install the reaction sun gear and transmission output shaft. Install the yellow lock ring onto the shaft to retain the reaction sun gear.
Install the appropriate thrust washer onto the low-reverse sprag hub and retain it with TransGel. Lightly lubricate the reaction sun gear spline, then align and install the reaction sun shell. Install the thrust washer inside the shell and retain it with a coating of TransGel.
Lightly lubricate and install the input planetary gear set assembly.
The entire reaction power path assembly is depicted here for reference, but refer to the transmission repair manual for specific instructions and details for each section.
Disassemble the input drive shell forward clutch, reverse clutch, sprag, direct clutch and inspect all parts.
Remove the lock ring from the 3-4 clutch backing plate, then the backing plate. Remove the 3-4 clutch steels and plates, apply plate, and retainer, being careful to maintain their order as removed. Inspect the steels and clutch plates as described above, and replace any parts as necessary.
Remove the lock ring for the forward (direct) clutch, then the backing plate. Remove the forward clutch steels and plates, the Belleville or waved plate, and the apply plate, and retainer, being careful to maintain their order as removed. Inspect the steels and clutch plates as described above, and replace any parts as necessary.
Remove the forward sprag clutch as an assembly. Mark the orientation so you know which direction is facing forward on reassembly.
Remove the overrunning clutch plates and steels. Inspect the steels and clutch plates as described above, and replace any parts as necessary.
Compress the overrunning clutch hub against the spring and remove the shaft lock ring at the hub. Relax the compression and remove the overrunning clutch apply and forward clutch apply pistons. Lift out the forward clutch housing and spring package, and inspect the springs for damage, distortion, or breakage. Replace any parts as necessary.
Inspect the interior of the input drum (torque drive drum) for indications of the clutch steels wearing into the drum guides. Any grooves can cause clutch steels to stick and interfere with proper clutch engagement or release.
Replace seals and wipers as necessary before assembly. With all parts intact, reassemble them in reverse order. The steels for the overrunning clutch should be 0.089-0.094' thick after cleanup. Replace if necessary to maintain proper clutch stack thickness.
Inspect the forward sprag clutch. When viewed from the smaller hub side, the smaller splined hub should be able to turn clockwise with minimal effort, and should not be able to be turned counterclockwise with any amount of effort or force. If the sprag is intact, install it into the torque drum.
Assemble the forward (direct) clutch in reverse order of disassembly. When installed with the support plate and lock ring, the total clearance of the stack should be between 0.030 and 0.063' as checked with a feeler gauge. Excessive clearance will cause clutch slippage, and inadequate clearance can cause poor release and burning of the clutch plates.
Assemble the 3-4 clutch and supports in reverse order of disassembly. When installed with the support plate and lock ring, the total clearance of the stack should be between 0.060 and 0.085' as checked with a feeler gauge.
The entire input power path assembly is depicted here for reference, but refer to the transmission repair manual for specific instructions and details for each section.
4l60e Identification
Install the input drum assembly onto the input planetary gear set and reaction sun shell. This can require some patience and dexterity, as it will be necessary to align and engage two sets of clutch plates with two different driven hubs. Rotating the input drum to help align the clutches makes the task possible, and up to seven plates on a stock clutch (you should have counted them) need to be aligned to allow full engagement.
Remove the lock ring for the reverse input clutch, then the backing plate, clutch plates and steels. Remove the Belleville (conical) plate, and inspect as previously directed for wear or damage and replace any parts as necessary. Compress the reverse input clutch spring and remove the retaining ring. Release the compression and remove the spring assembly and piston. Inspect and replace seals as required. Reassemble the piston, spring and retainer, then the clutch stack in the order it was removed. Install the backing plate and lock ring, and check the clutch clearance as previously described. Allowable clearance is 0.040-0.076' for the stack. Replace clutches or steels as necessary to maintain this clearance.
Inspect and replace the shaft seals on the input drum shaft. Inspect the input drum thrust bearing for damage.
Install the band.
Install the reverse input drum by aligning the clutch plates and rotating the drum as necessary to engage all the plates on the inner hub, as well as the outer fingers into the reaction sun shell.
Assemble and install the 2-4 servo from the outside of the transmission housing, making certain the clamp pin engages the band. Install the anchor pin for the stationary end of the band and retain it in place with masking tape.
PUMP
Remove the pump body bolts and split the pump halves. Remove the vanes and inspect for wear or damage. Lift out the vane backing rings and pump rotor and inspect for scoring on either face.
Inspect the pump cavity and end plates for wear of damage. Inspect the slew ring and springs closely (there are two concentric springs) for damage or distortion. Make sure the ring can pivot freely against the spring pressure. Replace any damaged or worn parts as necessary.
Drive the front pump bushing out of the housing bore with a suitable tool. The pump bushing supports the entire mass of the torque converter and can wear quickly. This is not an area to be overlooked. Press or drive a new pump bushing into the housing with a suitable tool.
Assemble the pump with new vanes or reverse the existing vanes if they are serviceable.
Lightly lubricate the pump rotor and vane support rings, and pack the pump cavity with TransGel or Vaseline to insure fluid pickup once the transmission starts to operate.
Align the pump halves with a band clamp tool and tighten the body bolts to 18 ft/lb. Lubricate the new pump bushing.
Install the pressure regulator valve into the pump housing. Install the thrust washer on the rear face of the pump housing and retain it in place with TransGel or Vaseline.
Install the pump into the front of the transmission making sure the gasket is aligned properly, and the pump bushings clear the input shaft without being damaged. Tighten the body bolts to 18 ft/lb.
The pump housing will only orient one way, since there is only one area of the pump which has two bolts close together. The orientation is self explanatory if you observe the bolt pattern.
There are M10 studs used professionally to help align the pump body for installation, but careful alignment will be sufficient.
At this point the transmission should be a nearly complete unit minus the valve body. You should be able to turn the turbine (input) shaft clockwise and the internal drag may drive the output shaft in the same direction. Turning the input shaft counterclockwise will be more difficult, and should result in an opposite rotation of the output shaft. If the input (turbine) shaft does not react as described, the input sprag may be installed incorrectly or damaged. Check and rectify this before proceeding further.
There should be between 0.015-0.036' total end play (axial) in the input shaft. Less than that can mean the pump is being bound or a clutch is not fully engaged, and more than that can mean wear in a drum or thrust washer/bearing which will require shimming. Shim washers are typically placed behind the thrust bearing on the input drum before the reverse input clutch and drum are installed.
VALVE BODY
Valve body rebuilding will not be covered in detail, since there are several variations. If you suspect valve body damage, you can remove solenoids and valve spools to inspect them and their bores. Repairs are typically done by reaming the bore larger, honing, or installing a wear sleeve after reaming, then honing to a finished bore size. Scuffed or damaged spools must be replaced.
Aside from rebuilding the valve body, the solenoids should be tested, along with the temperature sensor and pressure sensors. A plain ohmmeter will be sufficient. Your transmission service manual should list the appropriate resistances for the solenoid coils, and normal states of the pressure switches.
The separator plate should also be inspected closely where the check balls seal. Repeated operation of the checks will cause the balls to actually pein the openings in the stamped steel plate until the holes are distorted and enlarged. Given enough wear, the balls can go through the plate and render the check system ineffective. That can completely lock the transmission depending upon which valves are involved. Any wear should be addressed. The plate can either be replaced or repaired. Hard inserts are available to replace the worn areas. Larger check balls can also be used, but 0.285' is about the safe diameter limit so that the balls do not interfere with flow in the forward direction.
Install the single loose upper check ball and accumulator spring, and check that the caged check ball is still in the proper location.
Install the upper separator plate gasket and plate. Set the lower gasket onto the separator plate.
Clean the valve body and insert the lower body check balls in their appropriate locations.
NOTE: Two balls share one channel near the center of the valve body.
Retain the balls in their respective holes or channels with TransGel or Vaseline.
Install the stamped steel plate on the left rear corner of the separator plate and the accumulator body on the right rear corner of the plate. Insert a few other valve body bolts in various locations to align the gasket and plate properly, then tighten the three M6 X 18 hex head cap screws for the stamped steel plate to 100 in/lb, or about 8 ft/lb.
Tighten the two M6 X 35 and one M6 X 65 hex cap screws for the accumulator to the same torque specification.
Pass the transmission main electrical connector through the hole in the case and fold the wiring harness out of the way. Insert the linkage rod to the manual valve spool, then position the lower valve body and install all fasteners in their appropriate positions.
Torque all bolts to 100 in/lb.
Connect the electrical connectors to the appropriate solenoids and install the TCC solenoid and valve. Torque those two bolts to 100 in/lb. Insert the TCC PWM Signal solenoid valve into the remaining valve body bore and clip it in position. Snap the wiring harness conduit to the valve body bolts. Install the shift linkage detent arm spring and roller.
FINAL ASSEMBLY
Install a new filter and seal, clean the pan and magnet, and install it the oil pan.
This would also be a good time to install a drain plug in the pan to ease any future service and routine maintenance.
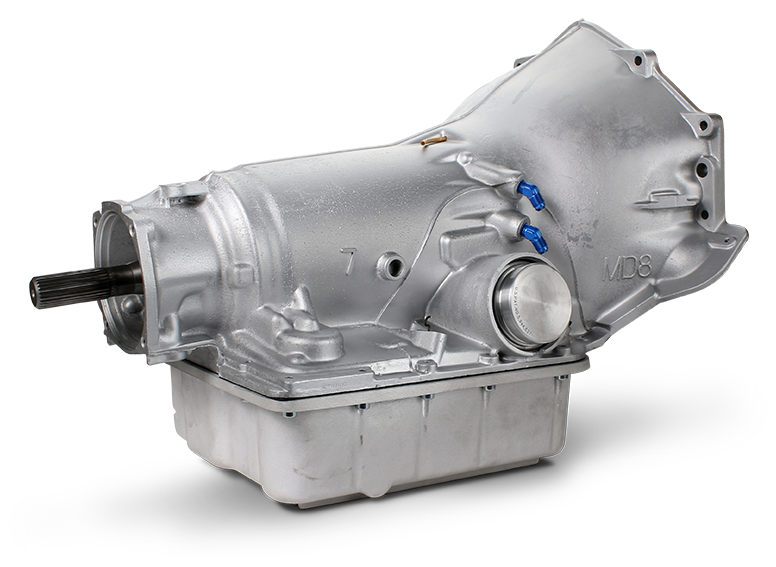
Set the transmission on the pan and install the adapter bell housing.
Torque all the bell mounting fasteners to 45 ft/lb.
Seal the main transmission electrical connector, oil cooler openings, vent tube, and input shaft and output shaft areas, then clean the transmission exterior.

Inspect the transmission case seal for the transfer case adapter or the tailshaft housing, and replace the seal as necessary.
If appropriate, replace the rear bushing in the tailshaft housing and install a new driveshaft yoke seal. Install the tailshaft housing and seal the end with a suitable cap.
The transmission can now be painted and have a new alpha label installed.
In preparation for installation into the vehicle, it would also be good to clean the cross member, lines, and vehicle wiring harness.
Applying antiseize compound to engine fasteners, chassis and mount bolts, exhaust studs, and other various fasteners is always prudent.
If it has not already been done, drain the torque converter completely. Tip it, slosh it, agitate it, and do whatever is necessary to get all you can out of the converter housing. A typical converter contains several quarts of fluid, and any contamination which resulted from the transmission failure is likely in the oil within the converter. Draining it as much as practical reduces the contamination the new filter will experience and helps insure a successful repair.
When the bulk of the oil is drained from the converter, placing it upside-down over a large steel container (a coffee can works great for this) will allow nearly all the remaining oil to drain out over several hours.
You should also inspect the hub of the converter for visible wear. This is the part which mates the pump bushing, and they are common wear areas.
If the converter has high mileage, it may be better to replace it with a new or factory remanufactured unit. Read the Home page and PARTS and UPGRADES section for the full explanation.
Lubricate the front pump seal and pump bushing with TransGel or transmission fluid, then install the torque converter onto the transmission input shaft. There are two splines to be engaged, and one drive lug (the double slots on the main converter hub) to engage with the pump. Carefully align the converter with the input shaft and slide it into place. Rotate and lift/tilt the converter as necessary to engage the splines and pump drive lugs. When installed correctly, the converter should slide all the way back to the point where it contacts the adapter bell.
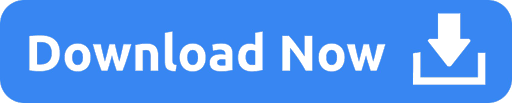